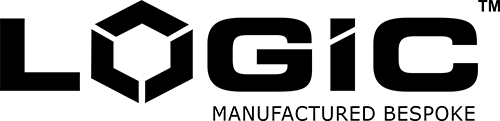
Corten vs. Stainless Steel vs. Powder Coat: A Comparison for Outdoor Design
When planning an outdoor space project that includes architectural steel elements, you typically have three choices: Corten (Weathering) Steel, Powder Coating, and Stainless Steel. It’s essential to understand the significant differences between these finishes, not just in terms of aesthetics but also in various other factors that can determine the success of your project. Here’s why:
Corten is closely related to Weathering Steel, often used interchangeably. It’s a robust steel grade initially developed for the American rail industry. What sets Corten apart is its unique rust-colored finish, a result of its various metallic elements like Copper, Nickel, Chromium, and Titanium. Unlike standard steel, Corten oxidizes when exposed to moisture but then “self-seals” after the initial oxidation, creating a distinct appearance. This transformation can take from 6 months to 2 years, depending on environmental conditions.
While Corten is excellent for specific environments, it has its pitfalls. It’s essential to specify Corten Grade A for external architectural use and consider the environmental conditions where it will be placed.
Powder Coating is an advanced method of painting steel.
Coloured polyester granules are applied as a free-flowing powder through an electrostatic charge, resulting in a uniform, hardwearing coating. The process involves three key steps: surface pre-treatment, powder application with a spray gun, and baking to create a durable finish.
For outdoor use, it’s crucial to protect the steel from corrosion during pre-treatment. Options include hot-dip galvanizing or zinc primer, though the latter is considered less effective.
Stainless Steel is a corrosion-resistant alloy due to its Chromium, Copper, Titanium, Molybdenum, and other elements. Common grades for outdoor architectural use are Grade 304 and Grade 316, both containing at least 11% Chromium.
Stainless Steel offers various finishes, including Mill, Brushed, Satin, High Polish, and Bead Blasted, providing flexibility in design.
Corten Pros:
Corten Cons:
PPC Pros:
PPC Cons:
Stainless Pros:
Stainless Cons:
Conclusion:
Choosing between Corten, Stainless Steel, or Powder Coat depends on the specific project and its surroundings. For post-industrial settings like refurbished warehouses, Corten can be a great choice. New build residential blocks might benefit from a powder-coated finish that matches the overall aesthetic, while prestigious areas may find Stainless Steel adds a final touch of elegance.
Ultimately, there’s no one-size-fits-all answer – it’s about assessing each project’s unique requirements and selecting the most suitable option.
https://www.accoatings.co.uk/powdercoatings/
https://www.powdercoating.org/page/WhatIsPC
http://powder-coatings.co.uk/facilities/guide/
https://en.wikipedia.org/wiki/Powder_coating
https://www.stainless-structurals.com/blog/stainless-product/common-finishes-stainless-steel/
https://www.archtoolbox.com/materials-systems/metals/stainless-steel-finishing.html
https://fractory.com/stainless-steel-finishes-din-astm/
https://en.wikipedia.org/wiki/SAE_steel_grades
https://www.aalco.co.uk/datasheets/Stainless-Steel-Surface-Finishes–Polishing_135.ashx