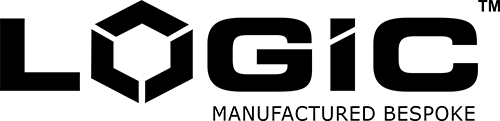
Steel, one of the most widely recycled materials, plays a crucial role in reducing environmental impact. In fact, an impressive 80% of the UK’s scrap steel is recycled, making it a global leader in sustainable steel practices, in stark contrast to the US, where only 50% is recycled.
In contrast, steel recycling involves collecting and processing discarded steel products and scrap and melting them down to create new steel. This process consumes significantly less energy and reduces the need for mining and refining iron ore. Recycled steel not only saves resources but also decreases greenhouse gas emissions and other pollutants associated with steel production.
The global steel industry is responsible for a significant share, approximately 5-8%, of greenhouse gas emissions worldwide, making it one of the most polluting industrial sectors. To put it in perspective, producing 1 ton of steel results in around 1.8 tons of carbon dioxide emissions.
Energy Efficiency: The energy savings in recycling steel are substantial, with recycled steel using only about 25-30% of the energy required for virgin steel production. This results in a significant reduction in carbon emissions and a lower environmental footprint.
Reduced Resource Depletion: By reusing existing steel, we reduce the need to mine additional iron ore and other raw materials, helping preserve natural resources.
Waste Reduction: Steel recycling reduces the amount of steel waste in landfills and helps mitigate the environmental impact of steel disposal. It also lessens the need for landfills and associated ecological disruptions.
Contamination: Contaminants such as paints, coatings, and other materials on steel products can complicate recycling and may require energy-intensive cleaning processes.
Limited Availability: The availability of scrap steel for recycling can be inconsistent and dependent on factors such as consumer behaviours and the longevity of steel products.
Quality Variability: Can have variations in quality and properties, which may limit its use in specific applications.
Infrastructure and Technology: A robust infrastructure and advanced technology are necessary to facilitate efficient steel recycling, which may not be readily available in all regions.
Recycling steel has been practised primarily for economic reasons due to its inherent magnetism, making it easy to separate from other materials. Moreover, steel doesn’t undergo significant chemical property changes during recycling, enabling endless recycling possibilities. In theory, your car could be made from steel initially manufactured in 1950.
The real economic value of recycling steel lies in substantial cost savings in primary production. By recycling steel, you skip the energy-intensive blast furnace stage, leading to a remarkable 70% energy savings. For every 1 kg of recycled steel, you save 1.5 kg of CO2 emissions and 1.4 kg of iron ore. This is partly attributed to the higher efficiency of electric arc furnaces compared to blast furnaces. As a result, steel recycling is gaining popularity for its environmental benefits, in addition to economic incentives.
The electric arc furnace (EAF) method is the primary choice when recycling old steel, as it can incorporate more than 80% recycled steel in a single furnace load. In contrast, the basic oxygen steelmaking (BOF) process typically uses only 25% to 35% of scrap steel in its total load.
For further information visit the Knowledge Base or contact the Technical Team.
It’s estimated that a whopping 93% of waste steel can be recycled, offering significant room for improvement in reducing the steel industry’s environmental impact. The good news is that steel is highly recyclable, and a substantial portion of it already undergoes recycling.
In fact, we can guarantee that our steel-raised planter edging systems include a proportion of recycled steel. Since all recycled steel is melted down and reformed, it’s challenging to specify the exact proportion. Nonetheless, ensuring steel is recycled at the end of its lifespan is a promising step toward a more sustainable future.