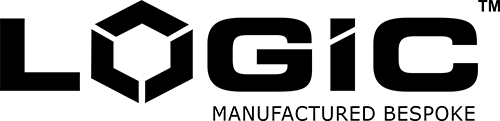
Is galvanising mild steel necessary? This article will discuss the factors that must be considered, especially related to external planter edging.
Understanding Galvanising for External Architecture
When dealing with steel in outdoor architectural projects, it’s crucial to grasp the ins and outs of galvanising – a process that prevents steel from rusting. In this article, we’ll explore when galvanising is necessary, the various galvanising techniques, and whether it’s cost-effective to skip this step.
What is Mild Steel?
Mild Steel is a highly versatile material used in various applications worldwide. In the context of outdoor environments and street furniture like benches and planters, mild steel is commonly used. However, it’s important to note that mild steel, being almost entirely composed of iron, is susceptible to corrosion when exposed to moisture. Hence, it requires protection.
When is Galvanising Necessary?
Galvanising is necessary in all cases when favoring a PPC Finish:
Raw mild steel exposed to moisture in the atmosphere will quickly oxidize and rust. Galvanising preserves its life.
Even if you plan to powder coat steel, galvanising is essential. While powder coating can provide a protective layer, any scratches or damage to the top coat can expose the steel to moisture and lead to rust. Galvanising ensures added protection.
When is Galvanising Not Necessary?
Challenges in Galvanising:
Degassing (Pinholing): Gas bubbles trapped in galvanized components can cause surface craters during the powder coating process. Pre-heating the component before powder coating expels these bubbles, ensuring a smooth finish.
White Rust: While a galvanized finish doesn’t rust, water puddles on it can lead to white chalky stains due to zinc oxidation. These stains are unsightly but don’t affect the steel’s structure.
Size Limitations: The size of a single part that can be galvanized is limited by the size of the zinc baths. For larger sections, components can be manufactured separately and assembled or subjected to ‘double-galvanizing,’ which may leave horizontal marks.
What is Galvanizing, and Hot vs. Cold Galvanizing?
Galvanizing comes in two main methods: ‘hot-dip’ and ‘cold’ galvanizing.
Cold Galvanizing involves painting raw steel with zinc-rich paint. While it bears the name ‘galvanizing,’ it’s different from the hot-dip method and offers limited long-term resistance due to being a surface coating. Typically, a polyester powder coating is applied for the desired color.
Hot-Dip Galvanizing immerses raw steel in molten zinc at around 450°C, leading to a metallurgically bonded zinc coating. This protective layer acts sacrificially, extending the steel’s durability. It doesn’t last indefinitely but offers robust protection for approximately 50 years.
Hot-dip galvanizing can be done before or after fabrication, depending on complexity. Post-fabrication galvanizing results in a rougher surface, while pre-galvanized steel has a smooth finish.
Conclusion
In conclusion, galvanising is essential for mild steel in outdoor architectural applications unless using Stainless Steel or Corten. To ensure the longevity of your finished product, always opt for galvanization when working with external mild steel.
https://en.wikipedia.org/wiki/Galvanization
https://en.wikipedia.org/wiki/Hot-dip_galvanization
https://en.wikipedia.org/wiki/Carbon_steel
https://www.metalsupermarkets.co.uk/what-is-mild-steel/
https://galvanizeit.org/knowledgebase/article/what-does-the-cold-galvanizing-process-consist-of
https://www.galvanizing.org.uk/galvanizing-process/
https://www.galvanizing.org.uk/galvanise-steel/
https://www.powdertechcorby.co.uk/about-us/our-process
https://monnigindustry.com/2020/08/18/can-you-powder-coat-galvanized-steel/