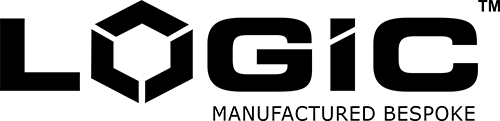
GRP refers to Glass(fibre) Reinforced Plastic and it is a composite material that consists of a polymer matrix and glass fibres. The polymer matrix, usually an epoxy/resin or similar, is the binder for the fibres in the structural laminate. The glass fibres add strength to the composite.
The manufacturing process of GRP is relatively simple. The glass fibres, or strands, or woven together with the resin to create a flexible fabric. GRP is a moulded product which means that it must be placed in a mould of the shape of the item it is required to take. This is important because it means it is very difficult to create bespoke shapes from GRP as each shape would require a new mould to be made first.
The emissions caused by the manufacturing of GRP are high – it is a processed product that goes through several production iterations. However, compared to materials like steel, the production of the base resins and then the ‘weaving’ process has a smaller total environmental impact.
There are three main reasons why GRP has become a mainstay for industrial purposes.
There are other desirable properties, but they are mainly related to industrial concerns such as non-conductivity.
Although it does have its advantages, GRP planters are not ideal for external use.
As mentioned above, one of the biggest problems is that GRP has to be moulded. Therefore it is only available in set section sizes with very little scope for bespoke/custom work. Also, there is the issue of fire risk. GRP is a flammable material. It will not melt like plastic, but it will burn. At roof or podium level, this can mean a breach of BSI 8579, which states “A balcony or terrace should not give rise to additional fire risk to a building or adjacent building by virtue of its existence”.
Finally, although boasting high impact resistance, GRP is susceptible to bending under load which isn’t a desirable characteristic for a bench.
GRP is inherently difficult to recycle. The very nature of the interwoven fibres means it is almost impossible to break them back down again. Therefore, most GRP ends up going to landfills. This is a big problem because 50kt of end-of-life GRP is created each year.
In conclusion, GRP properties lend themselves much better to industrial purposes. It is another question whether it should still be in use even for industrial purposes given that it can’t be recycled, but that will not be discussed here in any further detail.
Unfortunately, its weak points are very relevant to external furniture and planters, especially the poor fire resistance. For rooftop terraces and podiums in particular, this means that GRP options should not be considered, however cost-effective or lightweight.
For a more in-depth look into fire regulations, visit the Knowledge Base or book the Fire CPD – Are fire regulations destroying podium design?
https://www.materialstoday.com/carbon-fiber/features/recycling-glass-fibre-reinforced-composites/
https://www.recyclingwasteworld.co.uk/in-depth-article/composites-tough-materials-to-recycle/147052/
https://gripclad.co.uk/useful-information/what-is-grp/
https://www.amiblu.com/why-grp/